Bypassing the challenges of federal facility modernization
Outdated spaces put missions at risk, but improvements have been slow in coming.
Despite their value, building remodels and upgrades have not been a priority in Federal spaces for a long time. Many of these buildings are in sore need of repair and modernization. The worst of them are falling apart, and many others are lacking in features that could make them better. These outdated spaces inhibit mission readiness.
Because of the complexity and red tape involved in MILCON, construction projects can take up to a decade or more to finalize. By that point, the technology may already be obsolete. With the time and effort required, and the odds of any commander being able to see the project through to completion, it’s not surprising that other concerns frequently take priority.
These difficulties are compounded by the challenges of traditional construction and the many steps required to see a project to completion. These two inefficient processes have combined repeatedly to exacerbate the current infrastructure crisis facing the military today. But you don’t need to be locked into this way of doing things.
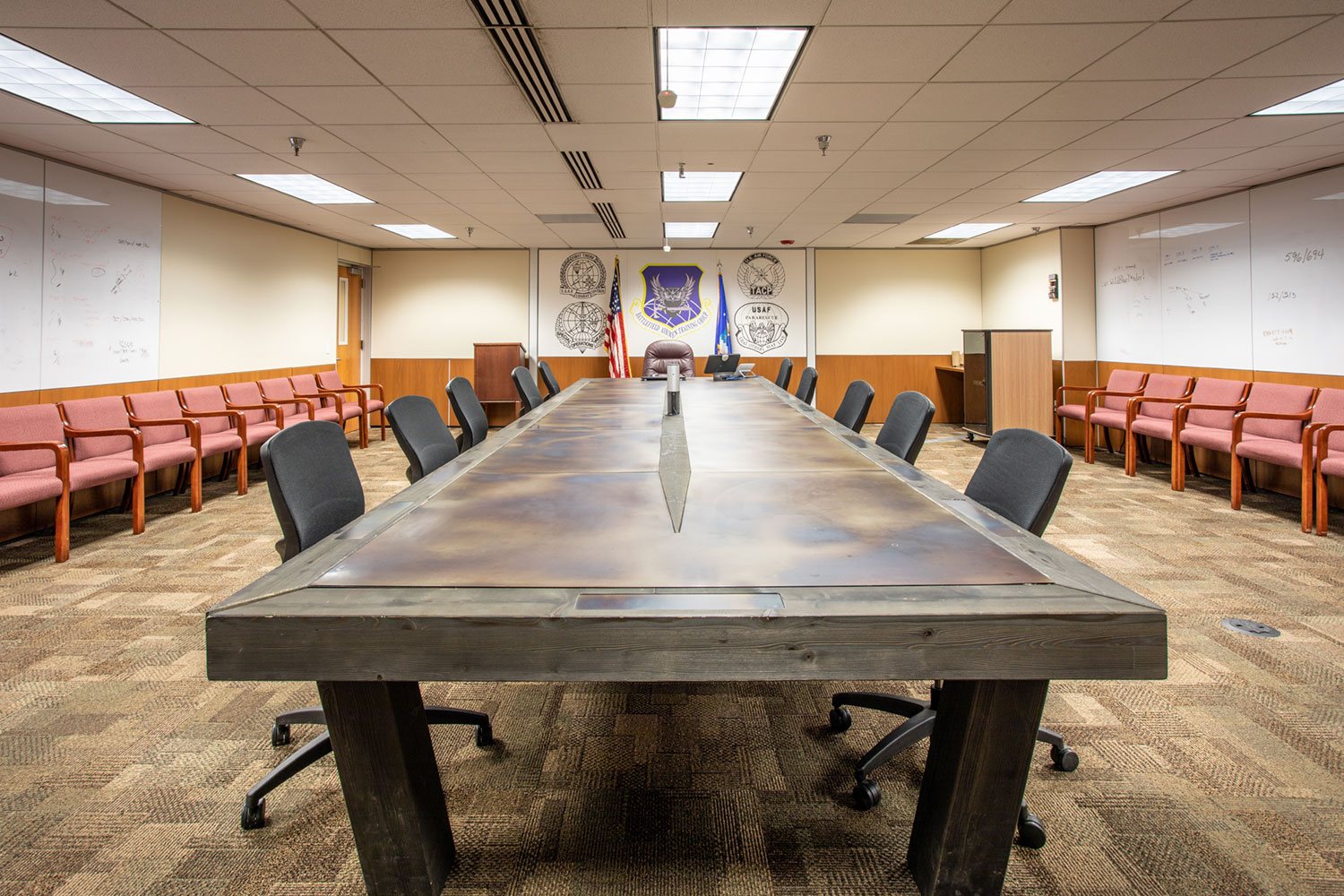
Strategic alternatives to traditional construction
What if buildings could be made with the same efficiency as cars? Systemized manufacturing connects design, fabrication, and construction into a streamlined process. That’s one of the cornerstones of what we do at Improve Group.
Our construction method utilizes systematized assemblies that let you pivot quickly to keep pace with the OPTEMPO and close the facility readiness gap. Offsite and modular construction cuts down on build time. These prefab components allow for swift installation, ease of planning, and relocatable and agile material construction. If the building can be as agile as your warfighters, it can support those mission capabilities.
Another strategy for streamlining construction is utilizing alternative procurement vehicles when available and appropriate. We have experience with SBIR (Small Business Innovation Research) and the OTA (Other Transactional Authority) as ways to orient funding around mission needs and minimize delays.
Security and collaboration
Conference rooms are not just places for one-way briefings. They are centers of collaboration and discussion, both for people in the room and in geographically separated units. But, as more conference rooms require SIPR and other classified communication systems, and are subject to the overall difficulty of facility modernization, these collaboration spaces often become outdated and non-functional.
To serve these modern needs, rooms should have the latest video conferencing systems, cameras, whiteboards, and other interactive technologies to facilitate better connection for all participants. Our modular modernization tech can provide the latest video systems for both secure and unsecured communications, better video systems to capture all participants, and flexible spaces that allow for formal briefs, group breakouts, and other functions.
Offices are mission critical
With the pressure on other mission-critical infrastructure, office modernization often falls to the bottom of facility modernization budgets. Too often, these technologically outdated offices aren’t set up for the way the new generation of warfighters and employees work.
To retain top talent, the spaces must match today’s expectations for better work environments. At the same time, every branch of the DOD understands that it’s about people first. When you prioritize the spaces where people spend the most time, it can lead to better retention, more productivity, and more innovation.
Our facility modernization system takes the headache out of construction by allowing easy phasing and the acquisition of interior wall systems, furniture, and technology. Our methods also can be accomplished in a fraction of the time of traditional construction and renovation. When the team is in a better space, they perform better, adding to overall unit performance.
Mission-focused solutions
We begin by taking a holistic look at the needs of the space and the mission it serves. All strategic decisions are made in alignment with the mission objectives. Through clear analytic data and objective-first thinking, we can help clarify the value of a project to the bigger picture, in order to clear a path for funding and approval.
By compressing design and construction together, you can plan with the intent to build immediately and cut down on time wasted. Agile construction techniques allow Federal buildings to adapt as necessary to meet the needs of the objective, making it possible to prioritize and complete renovations that may have otherwise been neglected. Buildings that move at the speed of change create facilities that are always mission ready.
More Insights
Design a better ending.
Call 800.244.1452
"*" indicates required fields